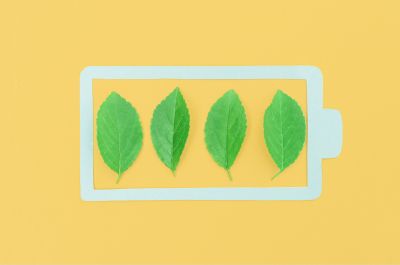
JETCELL project is aimed to redesign the anode of a Molten Hydroxide Direct Carbon Fuel Cell (MH-DCFC) through the exploitation of additive manufacturing flexibility and near free-of-constrain production by means of binder jetting technology. In a MH-DCFC cell, the anode represents the electrode where the carbonaceous fuel is oxidized liberating electrons and producing electricity. In the current configuration, the fuel cell is fed per batch, thus limiting the possibility of continuous working requiring the interruption of electrical connection to remove exhaust fuel. Thus, the design of an innovative anode capable to be fed continuously meanwhile evacuating the burn fuel is a challenge that must be faced, aiming at reaching the goal of carbon neutrality by scheduled time. Since binder jetting technology does not employ any thermal source to melt the powder bed, it is intrinsically capable to process metals, ceramics and composite materials. MH-DCFC are fed by carbonaceous materials, so that, to avoid fossil fuel consumption and CO2 generation, biogenic carbon will be used, obtained by the torrefaction or slow-pyrolysis of biomasses.
Specifically, olive pomace will be used as feedstock to obtain the biochar fuel. This will open new synergies between agricultural and power industries in the perspective of circular economy. Since the efficiency of DCFC can be augmented by the use of oxidic catalysts made by iron oxide, lime and magnesia, red muds will be also employed in cell design. By this choice, a specific use of this absolutely hazardous and environmental concerning waste can be defined, solving one of the biggest issues affecting the primary alumina industry. Metallic (AISI 316L stainless steel) and composite (AISI 316L+RM) anodes will be printed with several geometries (tea-bag and double helix DNA-like shape) and tested in a laboratory scale MH-DCFC cell with traditional configuration, currently using biochar as fuel. Furthermore, insulating-catalytic coating made by red mud will be deposited on the inner crucible walls to maximize the share of use of red mud within this technology. Expected results of the investigation are the possibility of producing anodes really capable to be fed and discharge continuously while exploiting the catalytic properties of the iron oxides contained in the red muds.
The Mechanical Department is the principal investigator of this project and is in charge of re-design the fuel cell anode by the use of binder jetting additive technology, produce and characterize the biochar fuel and run and control the performances of the self-build DCFC. The acrivities are supported by the Department of Industrial Engineering of Università di Trento.
The project is structured over two years and is funded by the PRIN-PNRR2022 call.