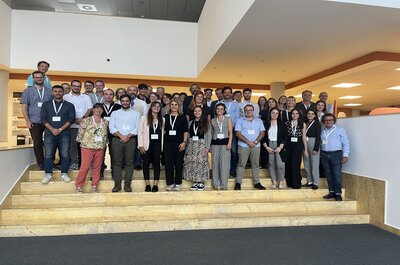
On September 12th and 13th of last September, the live meeting of the DeremCo project was held at the headquarters of Tecnalia (the project partner) in San Sebastian. The meeting represented an opportunity to assess the results achieved after 10 months from the start of the project, which aims to establish systemic Circular Economy solutions to unlock the reuse of composite materials and end-of-life components in new high-value-added products.
The Plenary Meeting was organized to showcase the progress of ongoing activities in the project, providing a comprehensive overview of future developments. Participants had the opportunity to discuss research results and explore each demo case in detail, gaining valuable insights into the project's evolution.
Furthermore, during the meeting, participants were given the opportunity to visit Tecnalia's facilities, seeing firsthand the laboratories and equipment used in their various research projects. These visits provided valuable information about the partner's capabilities and the practical aspects of their work.
"Composite recycling and re-use in high-added value applications is one of the major European challenges, potentially limiting growth in many strategic sectors," emphasizes Professor Marcello Colledani, coordinator of DeremCo. This visionary I3 project takes center stage in the pursuit of sustainable solutions for the complex issues posed by composite materials.
DeremCo started from a well-known situation. In the last years Glass Fibers Reinforced Plastics (GFRP) production is increasing of about 2% yearly, while Carbon Fibers Reinforced Plastics (CFRP) of 10-12%. Therefore, End of Life (EoL) waste stream is increasing, both regarding small consumption products (sports or design products) and large-scale infrastructures (as wind blades or construction wastes). In particular, EoL wind turbine waste flow is expected to be up to 30.000 tons per year between 2025 and 2030. Furthermore, the production of virgin carbon fibers is an energy-intensive process which consumes around 198-595 MJ/Kg. As a result, carbon fibers possess a much higher (approx. 10 times) embodied energy than other synthetic fibers such as glass. Recovering efficiently can hence significantly reduce their potential environmental impact.
GFRP and CFRP are currently treated following the European waste Directive 2008/98/EC. Most of the GFRP and CFRP waste is not systematically and properly separated. Landfilling is already forbidden in some EU countries and landfilling costs are going to increase significantly. Another active option is incineration and incorporation of ashes in the cement kiln route but it is not a profitable option and the residual value of the material is totally lost.
Specifically, DeremCo, whose extended title is “De-and Remanufacturing for Circular Economy Investments in the Composite Industry”, is a three-year-long project, whose purpose is to establish a systemic, cross-sectorial, Demand-Driven Circular Economy solution that will unlock the cost effective reuse of post-use composite materials and components in new high-added value products, grounding on the inter-relation between the technical and social eco-systems.
The project aims to have a twofold impact, both at the local and interregional levels. It is expected to have a positive impact on the environment, industry, consumers, and European society. In practical terms, the project will demonstrate the developed solutions with 14 different cross-sectorial industrial use-cases. These have been classified according to the required processes into two different pilot strategies for unlocking the potential of End-of-Life composite materials as manufacturing sources.
The first approach involves the use of mechanical processes, starting from end-of-life fiberglass products, to obtain recycled material pellets containing both fiber and polymer matrix, facilitating the production of various products for sectors such as automotive, energy, packaging, and sports. The goal is to reduce the use of virgin fibers while simultaneously increasing the concentration of recycled materials in these products up to 90%.
On the contrary, the second alternative, used to treat waste from fiberglass-reinforced composites and carbon fiber, is based on highly efficient pyrolysis processes to obtain long, clean, and mechanically high-performance fibers. As a result, they will be used for products suitable for the aerospace sector and markets with a strong demand for cost-effective carbon fibers, such as the automotive industry. These two alternatives, along with their respective demo cases, were the focal points of discussion during the two-day meeting, which was primarily structured around discussion sessions and roundtable talks.
The project involves different European areas characterized by the highest utilization of composites and based on complementarity in smart specialization on technical enablers, including Austria, Belgium, Finland, Italy, Portugal, Slovenia, and Spain.