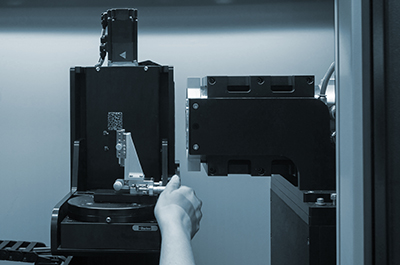
The Interdepartmental laboratory “Advanced MAnufacturing LAboratory” (AMALA) was established in 2014 at Politecnico di Milano by the joint efforts of the Departments of Aerospace Science and Technology, Chemistry, Materials and Chemical Engineering "Giulio Natta", Mechanical Engineering, and Civil and Environmental Engineering.
The need for AMALA raised from the observation that modern achievements in the most advanced engineering fields are called to satisfy increasingly stringent and integrated requirements.Structures must possess extreme efficiency and reliability while being operationally and ambiently durable and affordable, to guarantee operational lives of tens of years; they must be able to perform both structural and thermal tasks simultaneously, to ensure a sustainable economic operation.Furthermore, the production processes must be increasingly focused on environmental awareness, using raw materials and technologies with low energy consumption, recyclable or low impact materials and minimizing any type of pollution.Finally, the simultaneous satisfaction of these multiple requirements must not lead to weight or economic burdens.
The answer to such a complex request consists in the adoption of a multiplicity of materials, specialized but integrated with each other by means of new production technologies, sometimes very different from the conventional ones: these technologies are so linked to the production processes of the materials that they become indistinguishable from them.
AMALA enabled a systematic management of the skills already available within the university in these fields:
- fiber metal laminates
- smart structures
- auto-adaptive structures
- self-repairing materials
- shape memory alloys
- special crystalline structure materials
- functional/texturized surfaces
- functionally graded materials
- high energy content materials (propellants and solid fuels)
- expanded materials
The laboratory aims at being a benchmark in the sector of research on technologies for transforming, processing and characterizing advanced materials such as special alloys, composite materials and innovative polymers.With this in mind, AMALA Laboratory wishes to create synergies between the involved departments so as to set up a top tier center for the study of materials and advanced technologies in the aerospace, transport and bioengineering sectors, to become an authoritative interlocutor for the manufacturing industry in the competitive research market in this strategic sector.
AMALA Laboratory uses experience and equipment purchased by the departments involved in production and working technologies and characterization of structures and metallic, polymeric and composite materials.With the crucial contribution of the university, setting up AMALA Laboratory has allowed an X-ray computed microtomography (XCT) system for 3D X-ray surveys acquisition, available at Milano Bovisa Campus.
The collaboration between the members of the AMALA lab, and in particular the acquisition of the X-Ray CT system, has allowed several new researches. Here are some examples:
- The availability of the data gathered from XCT scans consents a detailed description of polymeric foams structure, then translated into a 3D finite element mesh which captures key geometric features while limiting the model complexity and the associated computational burden. Numerical models to consider their geometric structure, essential in defining the foam mechanical behavior together with the constituent material properties are then allowed.
- Porous asphalt is utilized as a wearing course on permeable pavement and on roadways to reduce aquaplaning and noise pollution. By investigating it with XCT, effective and total porosity as well as porous size distribution have been assessed and compared with results provided by laboratory rainfall simulations.
- Heterogeneous materials have great importance for rocket propulsion. Most of the energetic materials developed in this field feature peculiar microstructure that can be investigated for production defect identification (voids and particle debonding) and improvement of the formulation. A detailed volumetric characterization of energetic materials can be obtained and analyzed from XCT.
- The use of XCT allows to understand the mechanism of defects development in aluminium alloys components for automotive industry. More in general, the non-destructive study of defects in metallic components is allowed.
- Nowadays, adhesive bonded joints find large application in modern structures, especially for their lighter weight, lower stress concentration and better fatigue properties. Anyway, issues might arise from a multitude of different factors, which lead to local debonding and final unpredictable failure. Consequently, non-destructive testing is needed to assess the in-service state of the joints, particularly in the case of fatigue load conditions. Damage initiation and propagation can be successfully investigated using XCT.
- XCT has become the preferred tool to characterize additive manufacturing (AM) parts, as it allows to measure complex geometries and internal features, and to detect porosity without cutting the part. Open research questions in this field are focused on the effect of porosity (size and shape) on the final part properties, the final goal is to be able to predict mechanical properties based on the porosity structure found in the AM part. Furthermore, as the CAD way of representing conventional mechanical components is not effective when dealing with the complexity of AM, a pure volumetric way of representing an verify the geometry of parts is being investigated.